یک سال تلاش مهندسان پتروشیمی امیرکبیر در اجرای پروژه های تعمیراتی
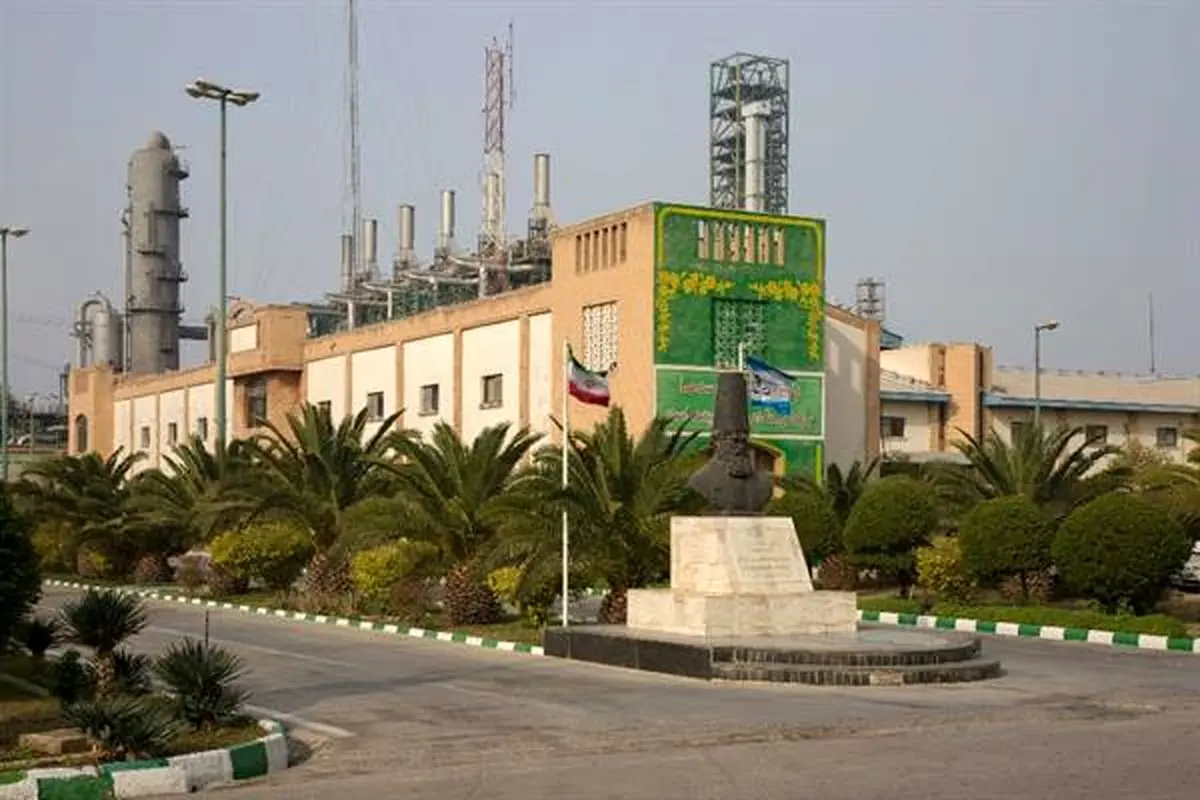
مدیر اداره تعمیرات شرکت پتروشیمی امیرکبیر گفت: در طول یک سال گذشته این اداره در حوزه منابع انسانی اقدام به بازنگری چارت سازمانی و تجمیع پیمانکاران نت در قالب یک قرارداد، در زمینه فرآیندهای کاری بهینهسازی فعالیتهای پیشگیرانه (PMO) و استقرار شاخصهای نت در سه سطح کرده است.
به گزارش ایلنا، محمدرضا حیاتی با تشریح اقدامات انجام شده در سال 98 اظهار داشت: در رابطه با ساختار سازمانی نیز واحد پایش وضعیت و ایجاد بخش کنترل مصرف قطعات ایجاد و کمیتههای RCA با هدف بررسی علل اولیه توقفات تجهیزات مهم نیز تشکیل شده است، استقرار ماژول اورهال و CBM در سیستم CMMSو ایجاد سیستمهای Prognost جهت اکسترودر واحدهای HD و LLD نیز در حوزه زیرساختی انجام شده است.
وی در ادامه با اشاره به اقدامات انجام شده به منظور بهبود شاخصهای عملیاتی خاطرنشان کرد: بهبود درصد هزینه نگهداری و تعمیرات نسبت به هزینه تولید از 14% به 16% و بهبود درصد قابلیت دسترسی فنی به فرآیند تولید از 98% به 99% از جمله اقداماتی است که با هدف بهبود شاخصهای عملیاتی انجام شده است، کنترل و در حال کاهش نرخ دوباره کاری فعالیتهای نت بین %4 تا 5% و بهبود نفر ساعت مصرفی فعالیتهای پیشگیرانه به اصلاحی از 39% به 41% از دیگر فعالیتها در این حوزه است.
مهندس حیاتی در ادامه به برنامههای عملیاتی میان مدت اداره تعمیرات اشاره کرد و گفت: برای ریشهیابی علل خرابیها(RCA)، میتوان به ایجاد چارت تخصصی RCA زیر نظر مدیر تولید و سنجش اثربخشی RCA اشاره کرد و در زمینه فرآیندهای نگهداشت نیز، نگهداری و تعمیرات مبتنی بر قابلیت اطمینان (RCM) قابل ذکر می باشند.
وی اضافه کرد: تکمیل طراحی اتاقهای روغن و تجهیز کارگاههای تعمیراتی و استقرار دستگاه تست High Pressure از موضوعات مورد اشاره در حوزه امکانات زیر ساختی است، در حوزه فرآیندهای بهبود نیز میتوان به استقرار ERP در سال 99 و انجام ممیزی نت و تدوین نقشه راه تعالی سازمان نت اشاره کرد.
این مسئول در بخش دیگری از صحبتهای خود به کارهای شاخص تعمیراتی انجام شده در طول یک سال گذشته اشاره کرد و گفت: اورهال سیستم LETDOWN SYSTEM از جمله این موارد است، این سیستم وظیفه تنظیم فشار بخار توربینهای اصلی واحد الفین را بهعهده دارد که در چهار سطح SHP، HP، MP و LP این کنترل را انجام میدهد و شامل تجهیزات کنترل ولوهای هیدرولیک در مسیرهای بخار، پنل هیدرولیک شامل تعداد زیادی سلونوئید ولو رابط بین اتاق کنترل و ولوهای هیدرولیک و مخزن روغن، پمپ روغن و لاینهای روغن ارتباطی میباشد.
وی ادامه داد: اورهال این سیستم بهدلیل عدم تامین سلونوئید ولوهای خارجی تاکنون انجام نشده بود و بعد از 15 سال برای اولین بار با تعمیر داخلی سلونوئید ولوها انجام شد. مشکل دوم در خصوص عدم تامین Toolsهای مورد نیاز جهت تعمیر این سیستم بوده است که باید تمیزکاری کلیه بخشهای این سیستم بهنحوی انجام گیرد که خلوص روغن به بالاترین حد ممکن (NAS3) برسد و این موضوع از طریق ساخت Tools داخلی انجام پذیرفت.
مهندس حیاتی تعمیر گیرباکس واحد LLD را یکی دیگر از کارهای شاخص تعمیراتی دانست و عنوان کرد: اکسترودر واحد LLD با ظرفیت 40 تن بر ساعت وظیفه تبدیل پودر پلیمر به گروانول را بهعهده دارد و شامل دو گیرباکس میباشد که گیرباکس شماره 2 مربوط به انتقال قدرت موتور به Melt Pump میباشد و در حین فرآیند تولید، دچار شکستگی چرخ دندههای آن شد.
مدیر اداره تعمیرات یادآور شد: بهدلیل عدم تامین قطعات داخلی گیرباکس از جمله چرخ دندهها، اورهال گیرباکس تاکنون انجام نشده بود و پس از 14 سال، تعمیر اساسی گیرباکس توسط پرسنل فنی داخلی انجام شد.
وی در این رابطه افزود: در مرحله اول به جهت جلوگیری از توقف تولید، بهجای Melt Pump دو عدد اسپول قرار داده شد و تولید واحد LLD از صفر به 27 تن بر ساعت افزایش یافت که 8 تن کمتر از ظرفیت نامی است. این مورد که بر اساس دستور سازنده بهجای 7 روز، در 4 شبانه روز با تلاش بخش فنی انجام گرفت.
مهندس حیاتی با اشاره به تعمیر کارتهای MD Controler سیستم Delta v خاطرنشان کرد: این کارتها مربوط به سیستم DCS واحد LD میباشند که وظیفه کنترل تمامی تجهیزات را بهعهده دارند، تامین کارتها بهدلیل تحریم عملاً امکان ناپذیر شده است و هزینه تعمیر توسط شرکتهای داخلی بسیار بالا و مقرون بهصرفه نیست، از این رو تعمیر کارتها از طریق Configure کردن، به ابتکار دو نفر از پرسنل فنی ابزاردقیق با هزینه چندین برابر کمتر، انجام و مورد استفاده مجدد قرار گرفت.
مدیر اداره تعمیرات، تعمیر اساسی گیرباکس LD و تعویض اسلایدولو را یکی دیگر از اقدامات شاخص در سال 98 برشمرد و عنوان کرد: داده برداری صحیح و آنالیز دقیق انجام شده روی روغن گیرباکس نشان از نیاز به تعمیر اساسی گیرباکس بوده است و عدم انجام آن میتوانست منجر به شکست کامل تجهیز و توقف طولانی مدت واحد گردد. اورهال گیرباکس تاکنون انجام نشده بود و پس از 9 سال، تعمیر اساسی گیرباکس توسط پرسنل فنی داخلی انجام شد.
وی افزود: جهت تعویض این تجهیز نیاز بود تا Screw اکسترودر که یک شافت مارپیچ بهطول 14 متر است، نیز خارج گردد که برای اولین بار بدون حضور Vendor انجام شد.
مهندس حیاتی در پایان خاطرنشان کرد: دادهبرداری صحیح و آنالیز دقیق انجام شده روی روغن گیرباکس نشان از نیاز به تعمیر اساسی گیرباکس بوده است و عدم انجام آن میتوانست منجر به شکست کامل تجهیز و توقف طولانی مدت واحد گردد.